Factory That Made Moldy, Barfy Recalled Tylenol Closes For Upgrades, 300 Lose Jobs
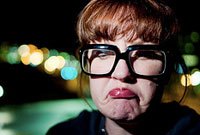
(effekt!)
Johnson & Johnson announced late yesterday that they will lay off most of the employees of the Philadelphia-area factory that produced the controversial musty, stinky pills recalled earlier this year. Staff have been on full pay and benefits since the plant shut down in April, but the controversial (that is: filthy) facility will close down for upgrades until some undefined point in 2011.
You may recall that the Food and Drug Administration investigated conditions at the plant and found bacteria in raw materials, poor quality controls, and general dirtiness.
According to the Wall Street Journal:
The company said in a statement that it will make a “significant investment” in refitting the plant and that it will be out of service for a “protracted period of time.”
…
Analysts say the Fort Washington plant might not reopen until the second half of next year, and the company could lose $500 million in revenue or more.
Aww, poor company. We’re sure that Johnson & Johnson executives have some real headaches because of all this. They should take some generic acetaminophen.
J&J Submits Plan to Fix Tylenol Plant Problems [Wall Street Journal]
PREVIOUSLY:
Johnson & Johnson Hit With Fraud And Racketeering Lawsuits Over Tylenol Recalls
FDA Announces Widespread Investigation Of McNeil After Tylenol Recalls
Johnson & Johnson Hit With Fraud And Racketeering Lawsuits Over Tylenol Recalls
Johnson & Johnson Hired Fake Shoppers To Buy Up Bad Motrin, Avoid Public Recall
Congress Opens Investigation Into Children’s Tylenol Recall
Criminal Charges Are Possible For Tylenol Recall Scandal
Want more consumer news? Visit our parent organization, Consumer Reports, for the latest on scams, recalls, and other consumer issues.